Introduction: DIY PCB Etching
PCB etching is the process that uses chemicals to make copper traces to connect different components on a circuit board. Copper is removed from the board except at the places where wired connections are present. The advantages include de-cluttering of the system and ease of seeing the connections and an increase in usability and portability.This tutorial would guide you through the process of etching your own copper board to make a PCB..
Step 1: Materials Required
1 board design(eagle)
1 OHP paper/transparent plastic sheet
1 clothes iron
Ferric chloride- 100gm
Acetone
UV sensitive Solder Mask
PCB Drill
Soldering Iron,Solder
Paper clips
Step 2: Designing Your PCB
You can design your PCB using Eagle. After designing the PCB in eagle, you would have two files, a board and a schematic.First remove the extra details from the board. Select the layer option and un-check all the fields that are not required like tplace, tname, torigin. tvalues. Now export the board file as an image. To do that open the board in eagle and then go to File>Export>Image. Select the monochrome option and save the image.
Step 3: Printing the PCB
Print the PCB on a transparent plastic sheet(OHP sheet) using a laser printer only. Before printing change the setting of the printer to highest resolution instead of higher speed in the pop up dialog box that appears on selecting the print option. If this setting is not selected, the toner would not transfer completely on the copper board.Open the image in paint and select all items and click invert colour. Save the image in a word file and print it.
P.S. Don't mirror the image before printing.
Step 4: Toner Transfer
Take the printout of the circuit and place it on a copper board with the printed side facing down. Now place a cotton cloth over it and heat it with an iron. First place the iron on the cloth and press vertically downwards without moving it sideways. After about 2 minutes gently move the iron and applying force. Do this for 4 minutes for a small board and 8 minutes for a medium sized one. Don’t move the iron too fast otherwise the print would be smudged. Let the board cool for 5 minutes then slowly remove the plastic sheet from one side.
Even if you don’t succeed in completely transferring the toner in your first try, don’t be disheartened as it takes time and practice to master this skill.
If you want to retry using the same board just use vim or other liquid detergent and a scrub to remove the toner and start again.
P.S. If there are any discontinuities on the board, use a black permanent marker to fill out those gaps.
P.P.S. Be generous in applying force while ironing.
Step 5: Etching
Prepare a solution of 40% w/w of ferric chloride.100 gm in 250 ml of water would suffice for etching two copper boards simultaneously. Dissolve the ferric chloride powder in warm water in small parts and stir continuously to dissolve it. Put the solution in a flat bottomed plastic container so that the copper board is covered in the solution when placed. Stir the mixture with a glass rod and shake the tray occasionally. The copper is first removed from the edges and then gradually from the center, so don’t place the whole board for a small PCB, cut the board to the required size before etching. It will take around 10-15 minutes to etch a PCB using the concentration specified. Remove the board using tongs and and place it under running water to remove the etchant. After this let it dry for some time.
Use acetone to remove the toner traces from the board. Prefer using acetone over isopropyl alcohol as the latter takes a lot of time and manpower to remove the toner.
P.S. FeCl3 is highly dangerous and corrosive. Always add ferric chloride to water and not the other way around. Don’t bring it in contact with your skin. Wear safety goggles while dissolving it in water. And finally don’t dispose it in the drain as it eats away the copper in the drainage pipes. Dispose it with a labs' hazardous waste or dilute it completely before throwing away.
Step 6: Solder Mask Application
You should apply solder mask to prevent the copper from rusting and to add a protective layer to the board. Before this step go to your saved board in eagle and change the layers setting such that only the pads are visible. Export it as an image and take its printout on a transparent paper. Now Take a UV sensitive solder mask and apply a thin film on the board on the board. Place the sheet with the darkened pads on top of the boards such that the pads align. Secure this with a paper clip. Place it under sunlight for 10-15. the solder mask would harden and then you can remove the sheet.
Step 7: Drilling
The next step is to drill holes for the pins of the electronics components. Use a PCB drilling machine and the drill bits of size corresponding to the width of the pins of components used. For common header pins use drill bits of size 0.7 mm . If the drill slips over the copper, first use a nail and a hammer to make a small impact on the place you want to drill. Then the drill bit wouldn’t move from its place. Keep the board on a wooden block during drilling as the drill bit passes through the board.
Step 8: Soldering
After drilling,place the components on the board such that the pins come out from the side the copper traces are present. Now use a soldering iron with a fine tip and use solder and flux to solder the pins to the board.
Step 9: Testing
After soldering use a multimeter in continuity mode to check if all the connections are continuous. To do this place one pin of the multimeter on a joint and place the other on the other end of the copper trace to which it is connected, if the multimeter beeps, the connection is correct. If there are any small discontinuities use solder to connect them or short them using external wires.
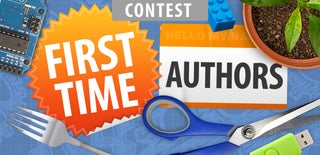
Participated in the
First Time Authors Contest 2016
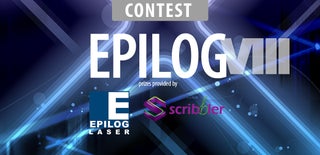
Participated in the
Epilog Contest 8