Introduction: Brake Drum Forge - Beginning Blacksmithing
About a year ago I decided that I wanted to try blacksmithing. To me, It seemed like an amazing hobby to pick up. The shaping and forming of metal meant that I could make any tool that I would need for any project. It also allowed me to use metal like no other tool could. I was fortunate enough to have an anvil already. All I needed was a forge...
Step 1: Materials
I picked up all the materials I needed from Menards and together they only cost me about $85
You will need:
- A 9 inch brake drum
- A 4 inch wide pipe flange that fits onto a 2 inch pipe
- Two threaded pipe nipples
- A 2 inch end cap (To catch the ashes)
- A 2 inch tee joint
- A foot long section of 2 inch steel pipe
- A 5 inch wide cast iron drain
- Bolts,nuts, and washers to hold stuff together
You will also need to run the forge:
- An old hairdryer
- Charcoal or coal to use as fuel
- 4 large cinder blocks to set it up on
Step 2: Assembly: Brake Drum
I was lucky enough to have the holes in my brake drum align with the holes in my pipe flange and cast iron drain. I simply put the drain in the inside of the drum, slid a bolt through, and secured that bolt with a washer and nut to the pipe flange. I decided only to use two bolts to secure this all together because only two of the holes lined up perfectly. You could use a drill to create your own holes but I didn't have one available when I made this.
Step 3: Assembly: the Pipes
To assemble the pipes you need to start by attaching the foot-long section of pipe to the side of the tee joint. This will be your air intake pipe. On the top and bottom of the tee join screw in your pipe nipples. On one of them, lightly screw on the end cap, This will catch ashes that fall from inside the forge and make it a lot easier to clean up.
After you have all the pipes put together I would recommend tightening them with a pipe wrench so that they don't fall apart when you have 2500 degree coals in them.
After your pipe assembly is tight, screw it onto the pipe flange that is at the bottom of the brake drum.
Step 4: Setting It Up
To set up the forge, I made two stacks each of two cinder blocks that were close together. I slide the air intake pipe through one of the holes in their sides and put a hairdryer into it.
To light the forge, fill it with charcoal (You could use coal but I use charcoal because it is cleaner), light the charcoal and turn on the hairdryer. Let it warm up for about 10 minutes before attempting to heat up metal in the fire.
Step 5: Make Anything
Now that you know how to make a forge that can heat metal to the point where it can easily be shaped, you can make anything! Make a tool, a decoration, a gift, whatever you want!
Please leave a comment telling me what you thought or asking any questions you have.
See you in my next instructable!
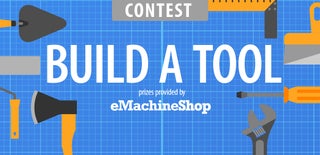
Participated in the
Build a Tool Contest 2017