Introduction: DIY Helping Hands for Soldering
Hello everyone! This build that I'm gonna be doing today came out of a need for either a circuit vise or helping hands to build and test DIY circuits. I had access to one at a local makerspace, but I needed one of my own so that I could do some tinkering at my home as well.
I checked the price online and found that it costs around 1200 INR. or 18.6 USD, which was way more than my expectations. On top of that, I had to buy a separate stand for my soldering iron as well.
I decided to give up on the helping hands, and instead bought a cheap 55 INR or 0.85 USD soldering stand from a local hobby shop. But the need for a pair of helping hands was still a requirement. In fact, they are an essential tool for soldering.
So I turned to one of the oldest toys that I possess: A Mechanix-4 Full Metal kit. It is comparable to a lego kit, and it was my most favourite toy as a kid, and still is, even after nearly 7-8 years.
Anyway, I thought that I could use some parts of it to make my own helping hands. The result is this instructable. And for a DIY item, it is pretty sturdy and works well for my requirement. And I put it together in half an hour only.
Although I have used the parts from a mechanix kit, it is not restricted to just this. You can use any material as long as it can bear a temperature ofup to 500 degrees Celsius without melting.
The best material to go for would be metals (E.g.: Aluminium L brackets) or hardwood of your choice. Do note that the clips that hold the PCB must be metal to be on the safe side. Do not use wooden clips for this purpose. Also, PLEASE don't 3D print parts for this, especially if you're just starting out. The soldering iron or molten solder may touch the part and ruin the stand, and also release some noxious fumes.
Disclaimer: This is in no way a replacement of a manufactured helping hand or circuit vise and is just made for fun and to test and see if my idea actually works. I use it for my regular work and it is doing well so far.
So let's jump right into it!!
Step 1: Parts List
The Tools required for this build are:
- A pair of Pliers
- A pair of Wire Strippers
- A Magnetic Screwdriver with a flathead bit ( any normal flathead screwdriver will do too)
- A soldering iron and soldering wire
- Glue Gun (optional)
The materials to be used in this build are:
- 3pcs 7-holed Mechanix part (equivalent dimensions: l: 3.5 in, w: 0.5 in)
- 3pcs 5-holed Mechanix part (equivalent dimensions: l: 2.5 in, w: 0.5 in)
- 4pcs 2-holed Mechanix L-bracket (equivalent dimension: l: 1 in, w: 0.5 in, angle: 90 deg)
- 7pcs zip ties
- 4mm heat shrink tubing (you can also use electrical tape)
- 3mm nuts and bolts
- Standard paper clips
- 2pcs 80mm stainless steel shafts
- 2pcs Alligator clips medium
- 1pc Soldering Stand
I've added equivalent dimensions for the mechanix parts so that those who may not have access to it can at least follow the dimensions for making their own parts. But it doesn't have to be the same size as the parts mentioned here.
Again, let me remind you, this is a suggestive list, please try to tweak it according to the things around you. And please leave a comment if you have any questions or suggestions.
Step 2: Moving the Spring Sideways
This step has to be done differently for left-handed and right-handed people. But it doesn't affect the rest of the build in any way.
So, depending on your hand preference, move the spring sideways (I'm moving it to the right because I'm right-handed) by loosening the bolt at the bottom of the spring, moving it to the side and then retightening it.
In my case, the bolt was loose enough for me to be able to move the spring simply by hand.
Step 3: Adding the "Body"
Now, take two L-brackets and attach them to the holes in the stand using the 3mm nuts and bolts. Now in my case, the holes were pre-existent, but that might not be the case for you. So in that case, grab a drill with a 3mm drill bit and drill the necessary holes, making sure to not get in the way of the spring.
WARNING: Be careful while drilling holes using a drill. Don't wear baggy clothes around drills, and if you have long hair, tie them behind before using a drill. Also, wear eye protection, since the chipped off material can fly off in any direction.
Nothing needs to be tightened as of now, just use your hands to tighten it lightly.
Now, take two of the 7-holed linear parts and attach them to the other side of the L-bracket with the 3mm nuts and bolts. There is no need for alignment just now. Leave it as it is, as we will tighten everything in the last part of the build.
Step 4: Adding the "Shoulder"
Attach a 5-holed part and two L-brackets to the top of the linear parts as shown. This acts as a "shoulder" to which the "arms" will be attached.
Don't tighten the screws too much on this part, because these will be the moving bits. When you mount the circuit, the shoulder's L-brackets will allow for it to be rotated along the plane of the linear pieces, which is helpful if, let's say, you want to solder two wires together.
Now, in my case, these metallic parts are made of ~1mm thick aluminium sheet (i think), so they are reasonably sturdy, but tend to get a little wobbly when a weight is applied to it. This is bad for soldering because you want the circuit to remain still while soldering. This is solved in the next step...
Step 5: Adding the "Skeleton"
To address the above-mentioned problem, I decided to add steel shafts about 3mm in diameter and 80mm in length as a support to the standing parts.
And the way I did it was pretty crude. I just used zip ties to basically keep the shaft and the linear part held together. And it works because the steel rods don't need to give it support, they're only there to increase rigidity so that the linear parts don't oscillate like a pendulum on applying force.
At this point, tighten the nuts and bolts at the lower L-brackets and the 7-holed linear part. Now you'll have a sturdy frame to support the shoulder and arms too.
Step 6: Attaching the "Arms"
Its time to attach the "arms". Use the nuts and bolts, again, keeping the connection not too tight. We're very close to the end now!
Just as a test, hold the arms and swivel them around a bit to check how tight or how loose everything is. You need to make sure that the base is tightly secured, but the arms and the shoulder joints must be just enough tight so that it can move with a little force from you.
Step 7: Prepping the Alligator Clips
Before we attach the alligator clips, we're going to give it an additional feature so as to make it easier to connect to the "arms" and also get an extra axis about which the clip may rotate, giving it more flexibility.
So first, we will take the standard paper clip, and one nut and bolt. Using a screwdriver and pliers, I tightly screwed the paper clip between the nut and the bolt. After that, I unfolded the paper clip as shown. I held the two free ends of the paper clip and, using the pliers, twisted them one time.
Now, I removed the nut and bolt from this modded paper clip, which leaves us with two loose ends and a ~3mm loop. I threaded the loose ends through a hole in the alligator clip so that the loop sticks out the back of the alligator clip. I wrapped the loose ends around the arm of the clip and then soldered it into place.
WARNING: Be careful with soldering anything, it is a bit dangerous. The iron reaches a temperature of ~350 deg C, which could cause serious burns and also scar fabrics and melt plastics. Don't be distracted around a soldering iron, and you'll be fine.
If you don't want to solder, you can use two-part epoxy to stick the pieces together. But again make sure that the glue or epoxy that you use will tolerate temperatures upto 500 deg C.
Repeat the above with another alligator clip and then we can proceed to the next step.
Step 8: Attaching the "Hands"
It is time to attach the "hands" to the "arms". The alligator clips have ~3mm loops sticking out of their backs after the previous step, which will help us attach the alligator clips to the 5 holed-linear "arms" using nuts and bolts. Keep this part loosely tightened as well.
And now with this step, your DIY helping hands are complete! They're super fun to make, and they're very cheap as well. Attach your pcb using the alligator clips and tinker away!
Step 9: Finishing Up and Further Ideas
Okay, so it was an easy enough build right? Now, what all can you add to it to make it even more awesome? I have a few ideas of my own, like, adding an additional LED to the build to illuminate circuits in poor lighting, a magnifying lens to aid in SMD soldering, even an adjustable fume-extractor. As you may have noticed, I already have some of the parts for these upgrades in the parts list already.
Apart from that, I also wanted to talk about the issues that I think can be resolved better. So as I mentioned earlier, I had to add steel shafts to prevent the parts from wobbling too much and so I did, but as you'll see in the video, it still wobbles a bit.
I think there are two reasons for that, the first one being that the steel shaft and the linear part are being held together by zip ties, so it doesn't completely stop it from wobbling. Although I should mention that I was applying a higher-than-normal amount of force to make it wobble.
Another reason is that the linear part is very long and very thin, so it behaves like a tuning fork, Instead, we need it to be in a more rigid shape, like an L-section or square tubing. But the major goal of this build was to make something cheap and easy to make, with parts that I had lying around.
So maybe in the future, I'll make an entirely new soldering stand with even more features and a stronger structure.
And of course, if you want, you can skip my way and use L-sections or square or even round pipes to make the structure less wobbly. In case you do, please share the photos in the comments!
Also, next time I would like to use winged nuts for holding the parts that are loosely held together, it just makes it much easier to tighten manually. Currently, it is a bit irritating to fiddle with the small nuts and bolts by hand. Again, implement that if you have access to these type of winged nuts.
That's it for this build, catch y'all later! :)
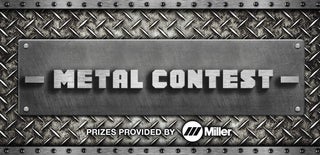
Participated in the
Metal Contest 2017
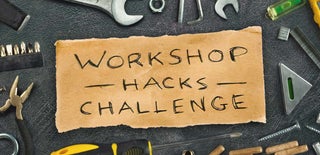
Participated in the
Workshop Hacks Challenge 2017