Introduction: Artisan Mallets for Leathercraft, Woodworking and Sculpting
There's an old saying that goes; "a craftsman/woman is only as good as his/her tools'. For me, that's only half the equation since, in my opinion, a crafter's greatest strength is in the ability to create his/her own equipment. To see a need, then conceptualize the piece of kit that would fill that need to perfection.
All of our modern tools had to come from somewhere. Some craftsman/woman, in a dusty garage or crowded workshop conceptualized it, then used their existing equipment to create a new, and better implement. It's unfortunate, in the technological age, that most of this creativity and insight that went into filling these needs has been set aside for assembly line created, machine made products that are all drawn from the same mold. Make no mistakes about it, the variety and quality of implements, on our store shelves, is amazing and a testament to human ingenuity. However, there's no greater pleasure than to create a tool to fit your hand...by your own hand... to fill any need that may arise in your own work.
In the spirit of creating my own tools, I wanted a high quality artisan mallet set that would encompass any project, from woodworking to leathercraft or for general use such as camping, or gardening. This meant they would have different weights, and shapes making them multi-purpose while, at the same time, remaining job specific. I decided on two fundamental types; the tinners mallet, which is the most common type with at 'T' shaped handle and head, and a round style, sometimes called a mason's mallet or a carvers mallet. Because there are different weight needs, I created 6oz and 8oz tinners mallets, and for the round mallet, I decided to create a 12oz and a 17oz heads. Instead of making two different round mallets, I decided to make a modular version where the handle is a spindle that secures optional round heads that can be changed to accommodate my needs. This allows for the creation of differently weighted and shaped heads without the need to make a new handle each time.
I had originally intended on splitting them into two different instructables, but since they are a 'set', I finally decided to make them into one how-to with different sections for each. The mallet set is made using several hardwoods I had around my shop. The tinners mallets were created with purpleheart for the heads, and oak for the shafts. The round mallets use maple for the heads, and a composite of zebra wood and purpleheart for the shaft. You can, of course, use a different type of wood, but beware of using soft wood, such as pine, spruce, or cedar, as these will not be strong enough to withstand repeated use.
Step 1: Tools and Supplies
Tools;
- Table Saw
- Wood Lathe
- Coping Saw
- Vernier Calipers
- Measuring Tape
- Drill Press or Drill and Bits
- 1/2" and 5/8" spade or forstner bits
- Wood Clamps
Supplies - Tinners Mallet;
- 1"x11" square hardwood stock for each mallet handle
- 1.5"x4" square hardwood stock for each mallet head
Supplies - Round Mallet;
- 1"x3"x3" hardwood pieces x4 for each round mallet head
- 1"x10" square hardwood stock for the handle
- 1.5"x4" hardwood stock for the top cap and base ring
- Dual Head Screw/machine screw + nuts and washers
Supplies - General;
- Wood Glue
- Sand paper - 150, 220, 400, 600
- Wood sealant or polish
Step 2: Turning the Handle - Tinners Mallet
There are three factors that go into the handle; comfort, weight and balance. All three of these factors can be addressed in the overall design.
Set your blank into your lathe, and reduce it until you have a dowel that is roughly 1" in diameter. Begin by reducing a 1" section, at one end, to a diameter of 1/2", tapering down from the dowel's overall diameter of 1". This will create the socket that will attach to the head. You'll want to leave a bit of material, on the end to accommodate the headstock mandrel which can be cut off later on.
The next section, to deal with, is the handle, which should be roughly 4" long with a concave curve in its center. This will act as a comfortable grip for you hand. Again, leave a bit of material at the end that can be cut off so that you can work the contour at the base of the handle.
Now, to address weight and balance, you should reduce the section between the socket end and the handle to a diameter of 5/8", leaving a 3/4" wide x 1" thick collar' between this section and the socket. This will help distribute the weight at the handle, and the head end, centering the balance directly between.
You can leave the handle plain, but it's a good idea to add some grooves to act as traction, on the handle. How many grooves you create is entirely up to you. For that I use the spear point parting tool, but the same grooves can be created using the diamond point as well.
When you're finished turning the shape of the handle, it's time to sand using progressively finer grits, and finishing with 600 wet paper. When that's complete, you can apply your sealant to the wood, ensuring you don't put any on the socket. You can also use my high grade beeswax polish which you can find here; High Grade Beeswax Polish
If you want a gloss version polish, you can mix the ratio of 1:1 solid beeswax to liquid oils and use the heat of the spinning lathe to buff it, forcing it to embed in the wood. This will give you all the protection of a Varathane sealant, but maintain a natural wood luster.
**Note** Test the feel and weight of your handle for comfort, balance and weight. You can always strategically remove material to balance it to your personal comfort.
Step 3: Turning the Handle - Round Mallet
The handle, for the round mallet is created in essentially the same way as the tinners mallet with a few small modifications. The handle section, itself is a bit longer, measuring roughly 6" long and the socket end is turned to a thickness of 3/4". Because it will act as the mandrel for the replaceable round heads, you'll need to make is long enough to accommodate the head, the spacer washer, minus the length required for the top cap.
The measurement, based on my listed material is as follows;
4"(head) + 1"(spacer washer) - 1"(top cap) - 1/4"(adjustment space) = 3 3/4" long
As you did before, you should cut some grooves to act as a hand grip, in the handle. When you're complete, sand accordingly then finish with your Varathane or polish, ensuring you don't put any on the mandrel end.
Finally, you'll need to drill a hole in the end of your mandrel to fit the double ended screw. To screw it in, tighten two nuts on the machine screw end and they will effectively lock together. You can then use a standard socket to thread it into your mandrel, leaving 1 3/4" sticking out. This will act as a fastening post that pulls the entire mallet together.
Step 4: The Spacer Washer and Top Cap - Round Mallet
The spacer washer and top cap were created out of the same piece of 1.5" x 3" block of turning stock.
The Spacer Washer;
The spacer is simply a 1" thick donut, created on the lathe. When it is cut from the blank, I set it into my drill press and used a 3/4" forstner bit to drill a hole in the center. After sanding and polishing, I glued it, securely, into position on the base of the mandrel. This will create a solid stopping point, for the head, when the mallet is screwed together.
The Top Cap;
The top cap is essentially a 1 1/2" x 1/2" thick, top piece, with a 1/2" long x 3/4" thick mandrel sticking out of it, and acts as a secure fastener for the head at the top of the mallet. A slight countersink lip is created in its top to house the washer and nut that will pull the mallet together. A hole is drilled directly through its center so that the double ended screw can pass through it. As usual, you should sand using progressively finer grit paper, and polish to seal the wood. Feel free to make this top cap as decorative as you want as it will be visible above the head of the mallet. I applied a small bevel to its top edge to give it a graduated tapered look.
Step 5: The Mallet Head - Tinners Mallet
Start by reducing your square 1.5" x 4" stock, on your lathe until its round. I generally like to reduce the material near the headstock and footstock mandrels, at this point, ensuring I am able to find the exact center of the head. Once the exact center is located, I remove it from the lathe, I set it into my drill press and drill a 1/2" hole that is 1" deep. The reason I like to drill the hole early is that finishing work will also clean the edges of the hole, ensuring that it is clean with no frayed material on its edges.
Reset your head into the lathe, and continue reducing it into your desired shape, and weight. You can remove it regularly and weigh it to ensure it is in the desired range. For my head, I removed my material from between the socket, and the face of each end equally, leaving a 3/4" lip to ensure strength. At this point you can set your handle, loosely, into the head and test its overall feel, keeping in mind that there is still excess material on the ends of the head. Check its balance, and feel until you are satisfied.
Once your head is done, sand accordingly and seal the wood with your sealant or wax polish, then you can remove it and cut off the excess material from each end, sanding them flat. Sealing the ends is optional, however I like to do it just to give it a 'finished' look.
Finally, insert glue into the socket, and around the end of the handle, then tap it into place, allowing it to dry for a full 24 hours prior to use to ensure a perfect bond.
Step 6: The Mallet Head - Round Mallet
The construction of this head is a bit different. We want the grain of the wood to be horizontal to the mallet itself for strength. To start, take your four, 1" thick x 3" x 3" blocks and glue them together, clamping them tightly and allow them to dry for several hours. Once they're dry, you can set the complete block into your lathe.
On occasion, I'll slice off the corners prior to turning, however on this small a piece it isn't necessary. With the speed of your lathe on slow and a good sharp gouge, you can make your piece round very easy.
Now, make no mistake about it, working with maple is like turning a block of granite. Especially so if you're going against the grain as this project requires you to. The positive side of that is that you'll end up with a mallet head that is extremely durable and will last a long time to come.
Keep turning your piece, removing it regularly to weigh it, minus an ounce for the core we will be drilling out later. The overall shape is tapered at one end (the bottom) and wider at its top end.
Once your head is complete, sand accordingly and apply your sealant.
To finish your piece, you'll need to drill a 3/4" hole straight through its core to house the mandrel of the handle. I generally prefer to drill half way through one end, then turn it over and continue through the other end. This way I can ensure the hole is straight through, and that no chipping occurs during the drilling process.
You can repeat this process as many times as you like to create as many round mallet heads as your desire, in different weights and shapes.
Step 7: Assembling the Round Mallet
Assembly is easy. Slide the head onto the mandrel of the handle. It should fit level with the spacer washer we installed earlier. The double ended screw should be protruding from the end. Now slide the top cap over the double ended screw so that its 3/4" post goes down into the opening of the head, meeting the mandrel end to end. The double ended screw should stick out roughly 1/4". If it doesn't, remove the head and adjust its height until it is at the desired height.
Once the top cap is in place, install the washer into the countersunk slot, then thread the nut onto the double ended screw, using a wrench to pull it together tightly.
Your round mallet should now be fully assembled.
Step 8: Finished
That's it. You should now have an awesome custom set of artisan mallets for all of your craft needs. With these basic designs, you can continue to create more and more pieces so that you, eventually, end up with a set so perfect it'll make your grandpa envious.
As usual, I hope you enjoyed the instructable and thanks for following.
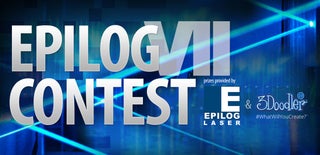
Runner Up in the
Epilog Contest VII