Introduction: DIY Self-Balancing One Wheel Vehicle
Interested in some of the trend of self balancing products such as segway and solowheel.
yes, you can go anywhere by riding your wheel without tiring. but it's great if you can have it yourself. Well, Let's Build It :)
Step 1: Ready Your Electric Motor
The first step of the project is the selection of the right motor, why? because this project we are required how to make electric vehicle with small dimension and light weight.
In this project I chose the Electric Hub-Motor, I suggest you to use hub-motor only because if using a standard motor you will need a complicated mechanical system. excess hub-motor here we no longer need to connect between motor and wheel use chain, because wheel and motor have become one unity. So, electric DC motor other than hub-motor is not recommended for this project.
Hub-motor that I choose with wheel size 14inch, I think enough for me because it fits with the ergonomics of Indonesian bodies.
Specification motor-hub = Power: 500watt, Voltage: 60v, Size: 14inch
Step 2: Designing Vehicle's Body (using 3D CAD Software)
At this step, it's time we put our imagination about vehicle body into 3D image. 3D model design before fabrication is very important, to minimize the occurrence of workmanship errors.
I need to make 3d drawing first because the manufacture of vehicle framework using CNC machine.
Well, on this project I have designed the vehicle body using Autodesk Inventor Professional. I'm sure you've used it too right? but if you do not have time to draw it, you can download some of my part files on my grabcad account.
Step 3: Making Frame (Aluminium Frame)
Manufacturing process of this project, I divide into three steps, the first is metalwork (Aluminium Frame), the second is nonmetal (PE Material), the last is body cover (PVC pipe material).
Now we start from metalwok (aluminium frame). Aluminum frame is the main frame of this vehicle, the weight of the rider will be supported by this aluminum frame, electronic laying and batteries are also mounted on this aluminum frame. You can look for aluminum material from junk shop, roughly you need some old aluminum:
1) 3mm aluminum sheet (80cm x 40cm) = used for electronics and battery place.
2) solid aluminum (14cm x 11cm x 5cm) = used for pedal holder.
This work you need a manual milling machine or cnc milling machine.
You can download the pedal holder file here : https://grabcad.com/library/pedal-holder-1
You can download the Plate frame file here : https://grabcad.com/library/self-balancing-unicyc...
Attachments
Step 4: Making Frame (Non Metal)
These non-metal frames are not as important as aluminum frames, but these non-metal frames that will beautify your one-wheel, are used as a body-cover holder and also has a handle that allows you to carry it everywhere.
The center of this part is mounted on the aluminum frame with 4mm nuts, then the side of this part will be installed body cover
You can download these parts here : https://grabcad.com/library/case-holder-self-bala...
Attachments
Step 5: Electrical System
The battery that used is Li-Ion battery with specification: voltage 60v and current 2200mAh, you can buy it from online store.
The electronics system that used in this project is the ARM Cortex F4 as a minimum system. Gyroscope and accelerometer sensors that integrated in the IMU sensor is used to obtain forward and backward balance of this vehicle. The driving circuit as the motor driver is the IRAM BLDC.
For detailed information about electrical system, you can refer to this paper for reference >> http://ieeexplore.ieee.org/document/7860971/
Location of IMU sensors installation on the vehicle, greatly affect for the balance, on this project the IMU sensors mounted on the aluminium frame and 4cm above the wheel axis.
the filter that use for the combination of gyroscope and accelerometer sensor is the Kalman filter,
please refer to my research paper about Kalman Filter >> http://ieeexplore.ieee.org/document/7861046/?sect...
Step 6: Programming - Balancing Test With No Rider
This balancing test with no rider, this test should be completed before driving
If the condition of the vehicle is still unstable like the video above, it means not to be ridden. You have to change the PID value in order to get the best result, the vehicle must be perfectly balanced before being ridden (marked with this vehicle stationary, not moving at all)
the software application used to program is the Keil uVision and Coocox IDE, I'm sure you already know it, for more details can visit here
http://www2.keil.com/mdk5/uvision/
http://www.coocox.org/software/coide.php
the filter that use for the combination of gyroscope and accelerometer sensor is the Kalman filter,
please refer to my research paper about Kalman Filter >> http://ieeexplore.ieee.org/document/7861046/?sect...
For detailed information about electrical system and control, you can refer to this paper for reference >> http://ieeexplore.ieee.org/document/7860971/
Step 7: Making Body-Cover From PVC Pipe, Mold From Plywood
The material used for this body-cover is PVC pipe that is flatten and shaped manually by burning process.
Ready your PVC pipe, some plywood sheets, and glue.
First you need to make a mold made from plywood, I suggest you cut the plywood using laser cutting because the result is better and more precise, otherwise you can cut it manually.
how to make it, first cut your pvc according to the required mold shape, then burn it until it can be molded and put on the mold, let it cool and stiff.
How to Flatten the Pvc Water Pipe for Making Any Stuff by burned, you can go to my friend's tutorial https://www.instructables.com/id/How-to-flatten-th...
Attachments
Step 8: Let's Ride
Let's Ride.. :)
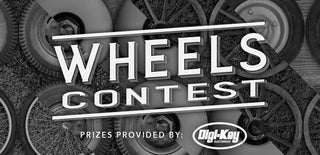
Second Prize in the
Wheels Contest 2017
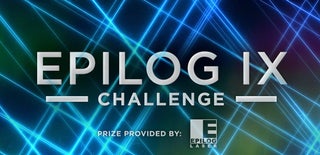
Participated in the
Epilog Challenge 9