Introduction: DIY Carving Knifes From Hacksaw Blades + Custom Box
In this Instructable I will be showing you guys how I made carving knives from all reclaimed materials and also a custom box to go with it.
For this set of carving knives I used old reciprocating saw blades for the blades of the knives and a 2 by 4 for the handle, and think overall they came out wonderfully! This is any incredibly inexpensive project to create and a great way to get you familiar with making simple knives, and getting used to working with wood and metal on a bench grinder. Even if you are buying all of the materials from scratch, a 2 by 4 only costs a couple dollars and the blades only cost around a dollar a piece, and you can easily get 2-3 carving knife blades out of every reciprocating saw blade. Also, please keep in mind that the techniques and processes that I use in this Instructable can also be used to create a full length hidden-tang knife and you would only have to change the dimensions of the blade and handle (or if you want to see exactly how I created a hidden-tang hunting knife you can find that Instructable on my profile page).
Materials for Carving Knives:
• Old Hacksaw blades (Or reciprocating saw blades)
• 2 by 4 (Or any handle material)
• 2-Part Epoxy
Materials for Custom Box:
• Plywood (I used 1/8th inch furniture grade plywood)
• Crafting Felt
• Leather strips or scraps
• Needle and Thread
• Brass Paper Fastener
• Decor Paper
Tools Needed:
• Jigsaw Dremel with Metal Cutoff Wheel
• Bench Grinder
• Xacto (for felt and leather)
*All of these tools aren’t necessary, but they just help make the process go quicker
Step 1: Designing the Blades
The first step for me was cleaning off the rust and paint from the old reciprocating saw blades, using a wire wheel on my bench grinder. This can also be done in a matter of minutes with just sandpaper because the blades are not very large.
The next step for me was researching which types of blades there are for carving, and then sketching out my designs onto the steel. I wanted to get a wide range of different carving knives, useful for different things, so I had a large variety of blades.
When designing, remember to account for the actual tang of the knife and make sure it is long enough that it will firmly hold in the handle of the knife. For me I included at least an inch or so, but figured that there won’t be all that much pressure on these knives (after all they won’t be used to split firewood or anything), and you can also put a pin through the handle and blade if you are worried it won’t be strong enough.
Step 2: Grinding the Blades
After I designed the blades I used a cut off disk on my Dremel to cut out each individual carving blade, then took them to the bench grinder and slowly and carefully ground them down to the outlines. I was very careful not to overheat them causing them to whatever heat treatment they had from the manufacturer, because I didn’t want to have very brittle blades, or very soft blades that can’t keep and edge.
This step can also be done with hand files, and since the blades are small and the metal is thin, it would take no more than 5 to 10 minutes per blade. Don’t think that just because you may not have the right tools that a project is impossible to do or out of your skill range.
Step 3: Making the Handles
Once I had finished grinding and shaping the profile of all of my carving knives, I began making the handles. For the handle material I used a pine 2 by 4, and traced out the rough outline of my handle contour onto the wood. Try to find straight grain with no imperfections such as knots, but it is really only for aesthetics because there won’t be too much pressure on this knife, and comfort is generally more important. Obviously you don’t need anything crazy such as straight-grain american hickory like you would need for an axe because axe handles need to withstand a whole bunch of force.
After I laid out exactly where I wanted the handles, I used my jigsaw to cut out the rough handles, and then used my jigsaw again to cut them in half so I could insert the blades. This step can also be done with a coping saw or any other handsaws you may have, it will just take longer.
After I had cut the handles, I traced the tang of the knife onto one side where I wanted it onto the wood. I then carved out the space where the blade would go with an Xacto, and made sure that the blade sat flush in the one side so that the handle could be glued together seamlessly. I then used 2 part epoxy to glue the blade in the handle, and to glue the two sides of the handle together.
Step 4: Shaping the Handles
The next step was shaping the handles with a bench grinder. This can also be done with a belt sander, files and rasps, or just sandpaper if you’re patient. I used the bench grinder to achieve a faceted look on the handles, which also make it very comfortable to hold and give good grip.
Once you are done sanding, you can also drill through the blade and the handle to pin the blade in and make sure it doesn’t come out, but that is only if you are afraid the tang might not hold well enough. Shaping is a hard process to explain because it all depends on what tools you have and the actual shape and style of the handles.
You could also stain the handles or put any finish you might like, but the bench grinder gave it a really cool burnt "patina" that I absolutely love the look of!
Step 5: Making a Box
After I finished the knives, I wanted to make a custom holding box for them, so I always know where they are and so the blades don’t get dulled or damaged from being just thrown in a toolbox.
I created the base of the box using all scraps from our recently renovated kitchen. I used 1/8 inch veneered plywood as the main box base, and glued all sides of the box together so that it created a completely sealed box. I then took it over to my table saw and set the fence about an inch and a half away from the blade, and cut all 4 sides of the box like that. This allowed me to have a box of perfect dimensions, which fit together perfectly. I then sanded a poly coat off of the plywood, and prepared the base of the box for the trim. I used all the same exact materials as the box for my Settlers of Catan project, and the only thing that changed was that the box was different dimensions. I also used the exact same stain and trim, and I love the outcome!
Step 6: Lining the Box and Adding Details
For the inside of the box I had lined it with red felt, which I think really gives it a clean and fancy look. It was still looking a little plain however, so I also added a custom piece of decorative paper, which I spray painted black. I thought it looked really awesome, and was a perfect touch to add an even more elegant look to the box. I’m not exactly sure where I got the paper from, or where you may be able to buy it, but if you have a Cricut, you should be able to cut out any background you would like (I have more information about the Cricut in my other Instructables).
Step 7: Leather Working and Brass Hardware
After I had lined the box, I then took scraps of leather I had gotten in a big bag from Michaels, and laid out my template for how l was going to hold the blades in the box. I found the perfect sized piece of leather to cut 2 equal width strips from, and cut that out using an Xacto.
Once I made 2 strips, I then joined the 2 ends and decided to stitch them together, and put that stitch in the middle of the box as an added detail. I could’ve tried to hide the split under one of the brass pins but I really like the look of it so I wanted to accentuate it. I took a thin nail, and punched holes in each of the pieces of leather, making sure they lined up, then quadrupled-up regular thread, and started sewing it together. There are special tools which are built for leather working made to do all of these jobs, but I don’t have any of them, so I just tried to be resourceful and use what I did have. After the pieces were stitched together, I then layed out all of the carving knives for spacing. I then fastened the leather to the felt by slitting a whole in both layers, then inserting in brass paper fasteners and folded them beneath the felt then glued them to the wood. I absolutely love the look of the rustic looking carving knives paired with the leather and brass hardware, with the ornate paper in the background.
This was the first time I had ever worked with leather, and I definitely don’t have any of the specialized tools, but for me it still worked out fine and I was thrilled with the result!
Step 8: Final Thoughts
This project was a first for me in many ways, and I learned a whole lot while completing it. It is made from all reclaimed materials, which I really love, and even if you can’t find all the materials reclaimed they are still even very inexpensive when new. This is a phenomenal learning project as an introduction to knife making and the methods and techniques used. The same techniques can be scaled up to create full sized knives, or you can see my other Instructable on creating a Hidden Tang Hunting Knife. Again, I really want to reiterate that this project can be done entirely with some simple hand tools, and that just because you may not have the right tools, please don’t think that a project is impossible to do or out of your skill range. Even for me this was one of the first times I had done a lot of the processes I show in the Instructable (I started these at the same time over the summer that I made my other knife), but I learned quickly and I think the final product came out wonderful!
If you like this, please vote for me in the contests this is submitted into, and also check out my other Instructables!
Thank you!
Brandon (16)
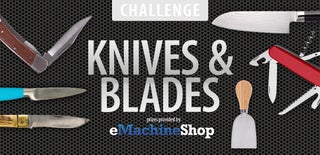
Grand Prize in the
Knives and Blades Challenge
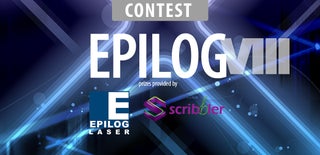
Participated in the
Epilog Contest 8
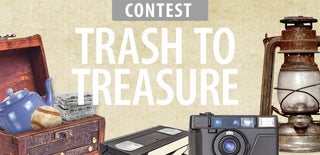
Participated in the
Trash to Treasure Contest 2017